Duynie is een bedrijf die afvalstromen verwerkt tot nieuwe producten. Voor Heineken in Mons en Bareoul is Duynie nu bezig om een verwerkingsfabriek, het Heineken Circle Project, te realiseren. Als automatiseringsspecialist is Paree al vanaf de eerste pilot bij het project betrokken.
Duynie ontwikkelde een duurzame methode om van de grote hoeveelheid restproduct granen, die na het bier brouwen overblijft, eiwitten en vezels te maken.
Bier bestaat uit de ingrediënten: gerst, hop, water en gist. Nadat alle processen voor het maken van bier zijn doorlopen blijven er restproducten achter, zoals bijvoorbeeld de granen, het zogenaamde Brewer’s Spent Grain. Dit restproduct wordt momenteel veelal verwerkt tot veevoer. Voor een 6-pack bier is al ongeveer een halve kilo graan nodig, waardoor er dus enorme hoeveelheden “afval” overblijven.
In de eerste pilot plant, die Duynie samen met Paree realiseerde, werd het restproduct uit de brouwerij in vrachtwagens aangevoerd en middels diverse machines verwerkt tot eiwitten en vezels. De resultaten waren goed en met deze kennis wordt nu de verwerkingsfabriek gebouwd op het terrein van de Heinekenbrouwerij in Mons en Bareoul (Frankrijk).
Duurzaam
Heineken heeft ambitieuze doelen als het gaat om het reduceren van zijn footprint, energieverbruik en afvalstromen. Met de realisatie van de verwerkingsfabriek, het Circle project, willen zij het volgende bereiken:
– Het winnen van eiwitten uit het graan restproduct;
– Het gebruiken van de gescheiden fibers als biomassa ter vervanging van de fossiele brandstoffen.
Weetjes Brewer's Spent Grain (BSG)
– Het restproduct BSG is ongeveer 85% van alle afvalstromen in brouwerijen;
– BSG wordt veelal gecomposteerd of gebruikt als veevoer
– BSG bederft snel vanwege het hoge gehalte water, suiker en proteïne. Hierdoor is het ook moeilijk te vervoeren en verder te verwerken;
– Iedere 6-pack gebrouwen bier, zorgt voor circa ½ kg BSG;
– Ongeveer 46 miljoen ton BSG wordt wereldwijd ieder jaar geproduceerd.
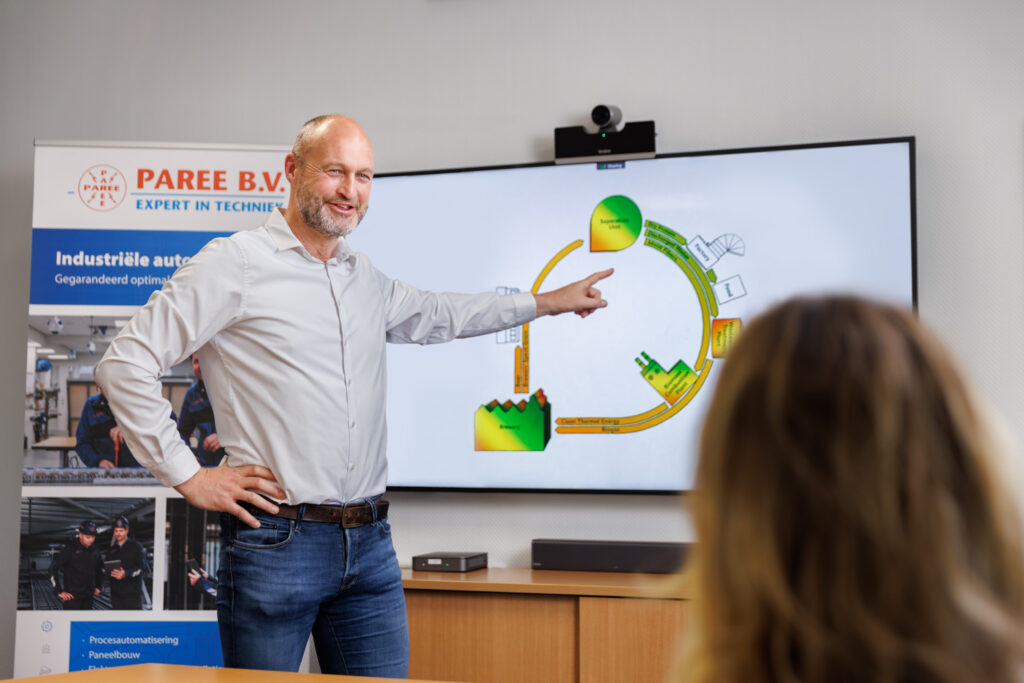
Het Circle proces
De nieuwbouw van de fabriek is gestart en medio 2025 zal deze in gebruik genomen worden. Anthony, project consultant Industriële automatisering, is al vanaf de pilot bij het project betrokken en legt beknopt uit hoe het Circle proces werkt.
“Het graan wordt via een pijpleiding van de brouwerij naar een silo in de verwerkingsfabriek getransporteerd. Daar wordt het product door diverse machines gesneden, gezeefd en gecentrifugeerd. Met als eindresultaat twee productstromen, een eiwitpasta en vezels, zeg maar het schilletje van het graan. De eiwitpasta wordt door een droger gestuurd waarbij het water verdampt en er een poeder overblijft, het eiwit. Dit wordt naar één van de vier silo’s getransporteerd, waarna een bulkvrachtwagen deze kan transporteren. Het andere restproduct, vezel, wordt gebruikt als biobrandstof voor de heet water boilers. Op deze manier is het restproduct volledig verwerkt en is de cirkel rond.”
Vanwege de voedselveiligheid wordt het gehele proces voorzien van een Clean in Place installatie waarbij alle silo’s, leidingen en verwerkingsmachines worden gereinigd.
Het Heineken Circle Project illustreert hoe innovatie en duurzaamheid hand in hand gaan. Een mooi voorbeeld van een gezamenlijke inspanning om de impact op het milieu te minimaliseren en tegelijkertijd efficiëntie te bevorderen.
Paree's rol
Paree verzorgt de automatisering van het project. Vanaf het voorstadium zijn we betrokken bij de ontwerpen van de installatie. Anthony vertelt: “Wij verrichtten de engineering vanaf een gedetailleerde componentenlijst. Deze lijst wordt uitgebreid met extra informatie en zo worden de componenten ingedeeld in zogenaamde typicals. Een typical is een soort gestandaardiseerde bouwsteen voor een bepaalde oplossing zoals bijvoorbeeld een frequentie geregelde motor. Vervolgens wordt de tekening gegenereerd met Typical Manager. Typical Manager is een softwareplatform die het ontwerpproces stroomlijnt door ‘typicals’ automatisch te genereren in een tekening.
In onze paneelbouw werkplaats worden de verspanende werkzaamheden uitgevoerd met een CNC gestuurde machine. Complete montageplaten worden door de machine automatisch geboord, getapt en eventueel voorzien van gaten. Hierna kan de paneelbouwer de onderdelen er direct op schroeven en kan gestart worden met de bedrading.”
Siemens PLC en SCADA
Anthony vervolgt: “Middels Siemens PLC besturing met Siemens Unified visualisatie software (SCADA) wordt deze fabriek tot leven gewekt. Vanuit een gecentraliseerde ruimte waarin de schakelkasten staan worden alle motoren aangestuurd, en veldcomponenten worden via lokale remote I/O kasten aangesloten. Alles verbonden met Profinet (ethernet).
Het SCADA pakket is een hele nieuwe versie van Siemens die volledig web-based draait, waardoor men via een browser (bijvoorbeeld Edge/Internet Explorer) verbinding kan maken met het systeem. Is ook voor Paree nieuw, maar superhandig omdat overal met internet, dus ook met een mobiele telefoon (mobile oplossing) SCADA kan worden geraadpleegd.”
Samen op weg naar duurzame brouwerijen
In het Heineken Circle Project speelt Anthony een belangrijke rol. Zijn betrokkenheid en samenwerking met projectmedewerkers van Heineken wereldwijd zijn cruciaal voor het succes van dit duurzame initiatief.
“Terwijl we nog druk bezig zijn met dit project, wordt er al gekeken welke Heineken fabriek de volgende zal zijn. Met de gestelde ambities en een kleine 200 brouwerijen wereldwijd zal het nog een drukke tijd worden. Een geweldige stap in de richting van een duurzame brouwerij-industrie.”